Freiform-Ersatzteil selber machen mit 3D-Scanner, Blender und 3D-Drucker
Ein Erfahrungsbericht: Wie ich mit Hilfe des Scanners Revopoint Mini und Blender erfolgreich ein beschädigtes Mini-Hirschgeweih restaurieren konnte

(Bild: pek)
Der Kühlschrankmagnet in Form einer kapitalen Hirschtrophäe misst gerade mal neun Zentimeter in der Höhe, begleitet mich aber schon seit dem letzten Jahrtausend von Wohnung zu Wohnung und findet jeweils seinen Platz oben an der Frontabdeckung der Gastherme. Er ist ein richtiges Pietätsstück – umso schmerzvoller, dass der einstige Zwölfender schon vor vielen Jahren seine rechte Mittelsprosse (so sagen die Jägersleute dazu, falls Wikipedia nicht lügt) verloren hat und seitdem seine Existenz leicht ramponiert fristen muss. Die genauen Umstände sind längst vergessen, das abgebrochene Teil ist verschwunden. Die helle Bruchstelle ist zwar nur wenige Millimeter groß, fällt aber auf.
Lange Zeit haben der Hirsch und ich damit gelebt, denn mir fiel keine Möglichkeit ein, das fehlende Teil zu rekonstruieren (außer ein winziges Stück Hartholz mühevoll passend zurechtzufeilen). Doch dann machte die 3D-Scanner-Technik einen Satz nach vorn und in der Redaktion fand sich als Testgerät ein Revopoint Mini ein. Der ist auf besonders kleine Gegenstände spezialisiert und löst 3D-Oberflächen bis zu 0,02 Millimeter fein auf. Ich wollte ohnehin mal ausprobieren, ob man damit 3D-Druckvorlagen von Ersatzteilen erstellen kann, speziell solche mit freier Form ohne klare Kanten. Deshalb fasste ich den Plan, damit die Bruchstelle in 3D zu scannen und dann auf dieser Grundlage eine Rekonstruktion des fehlenden Endes mit meiner 3D-Lieblingssoftware Blender zu versuchen.
Scannen
Seit dem Test hatte ich den Revopoint Mini nicht mehr an meinen Arbeitsrechner angeschlossen, daher stand zu Beginn erst einmal der Download und die Installation einer neuen Version der Scannersoftware an. Die sieht jetzt komplett anders aus als im vergangenen Jahr, als der Mini neu auf dem Markt war und wir unser Vorstellungsvideo dazu gedreht haben.
Empfohlener redaktioneller Inhalt
Mit Ihrer Zustimmmung wird hier ein externes YouTube-Video (Google Ireland Limited) geladen.
Ich bin damit einverstanden, dass mir externe Inhalte angezeigt werden. Damit können personenbezogene Daten an Drittplattformen (Google Ireland Limited) übermittelt werden. Mehr dazu in unserer Datenschutzerklärung.
Rundheraus gesagt, ist die neue Software (Revo Scan 5) ein großer Fortschritt gegenüber der Vorversion und sehr einfach zu bedienen. Auffälligster Unterschied: Will man einen Gegenstand in mehreren Durchgängen in unterschiedlichen Ausrichtungen auf dem Drehteller scannen, so versuchte die alte Software-Version, den neuen Scan mit den jeweiligen vorigen Durchgängen automatisch und in Echtzeit zur Deckung zu bringen (im Video zu sehen etwa ab Minute 7:45). Das klappte zwar oft und sah beeindruckend aus, manchmal schlug es aber fehl, und man musste komplett von vorne beginnen.
In der neuen Version der Software fertigt man stattdessen nacheinander die einzelnen Scans an und kann sie anschließend alle einzeln oder per Stapelverarbeitung von Artefakten säubern, die Punktwolken eindampfen und vereinfachen, bevor man die Software die 3D-Daten aller Scans automatisch zueinander ausrichten und daraus das finale Oberflächengitter berechnen lässt (siehe Bilderstrecke).
Ersatzteile selber machen: 3D-scannen mit Revo Scan (6 Bilder)
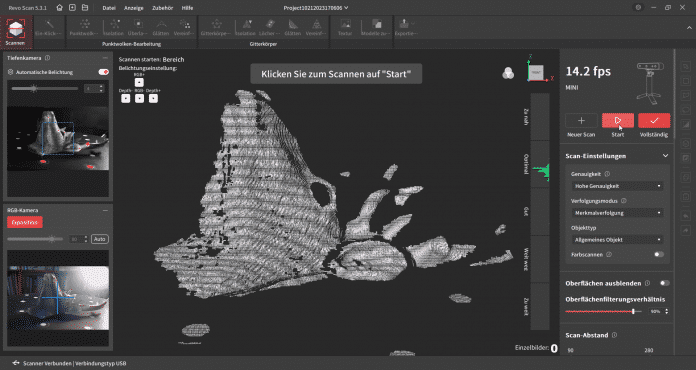
Ich gebe zu, dass ich bei diesem Scan sehr darauf fokussiert war, dass sich vor allem die Bruchstelle gut in 3D abzeichnet. Deshalb machte mir nicht die Mühe, so lange mit den Punktwolken-Filterfunktionen in der Scan-Software zu experimentieren, dass ein Artefakt-freies 3D-Modell des Hirschs exportiert wurde. Nicht, dass hier ein falsches Bild von der Qualität des Scanners entsteht: Die ist wirklich gut.
Rekonstruieren
Für 3D-Konstruktionen nehme ich bevorzugt die Open-Source-Software Blender und speziell für 3D-Druckprojekte habe ich mir mal eine Template-Datei angelegt, bei der die Grundeinheiten auf Millimeter voreingestellt sind (bei Blender entspricht die Standard-Einheit sonst einem Meter). Das hat unter anderem den Vorteil, dass exportierte STL-Dateien in der richtigen Größenordnung im Slicer für den 3D-Drucker auftauchen. Analog gilt das auch für den Import.
Die aus Revo Scan exportiere STL-Datei des Hirschs bestand aus fast 1,8 Millionen Dreiecken und war satte 85 Megabyte groß. Die importierte ich in Blender. Dank meiner vorher geöffneten Template-Datei und der Tatsache, dass der Revopoint Mini zuverlässig auch die absolute Größe von gescannten Objekten erfasst, brauchte ich mich nicht mehr um Skalierungen zu kümmern – ein enormer Vorteil des Lichtmusterverfahrens gegenüber dem ebenfalls denkbaren Verfahren der Photogrammetrie zur Erfassung von 3D-Formen.
Nur die Ausrichtung des Hirschs im Raum musste ich noch von Hand erledigen. Im Object-Mode schob ich ihn in die Mitte des Blender-Welt-Koordinatensystems und richtete ihn so aus, dass seine flache Magnetrückseite auf der X-Y-Grundebene in Blender zu liegen kam.
Alternative Modellierwege
Jetzt stand die grundsätzliche Entscheidung an, wie ich weiter vorgehen wollte. Eine Möglichkeit wäre, eine Kopie der Bruchfläche zu erstellen (alleine dafür gibt es in Blender eine ganze Reihe von Möglichkeiten), dann bei der isolierten Bruchfläche den äußeren Rand der Fläche auszuwählen und den dann mittels vielfacher Extrusion, Rotation und Skalierung zu einem Geweihende zu formen.
Weil das zwar relativ einfach klingt, aber meiner Erfahrung nach am Ende doch viel länger dauert als gedacht, bis die neue Mittelsprosse ansprechend aussieht und vor allem zur Formensprache des übrigen Geweihs passt, entschied ich mich für einen anderen Weg: Ich wollte versuchen, die gegenüberliegende linke und noch unversehrte Mittelsprosse des Geweihs als Blaupause für das Ersatzteil zu nutzen.
Dummerweise hatte ich beim Export des Scans nicht auf diesen Bereich des Geweihs geachtet, und ausgerechnet rund um die linken Mittelsprosse ballten sich Wolken aus Artefakten. Die waren aber schnell entfernt, wie man in der Bilderstrecke Schritt für Schritt sieht.
Ersatzteile selber machen: 3D-Scans von Artefakten befreien mit Blender (5 Bilder)

Spiegeltrick
Ich wechselte nach der Säuberungsaktion wieder in den Object-Mode und kopierte den Hirsch kurzerhand an identischer Position (Shitf+D, dann ESC). Im Outliner blendete ich den ersten Hirsch aus und fügte über Shift+A und Auswahl von Mesh/Cube aus dem Kontextmenü eine Quader hinzu. Der war erst mal mit zwei Millimetern Kantenlänge winzig, mit der Taste S und Ziehen der Maus brachte ich ihn auf ein paar Zentimetern Größe, rotierte und verschob ihn dann so, dass er möglichst viel von der Hirschkopie verdeckte, aber ein kleines Stück Geweihstange samt der linken Mittelsprosse außerhalb des Würfels sehen ließ (siehe Bilderstrecke).
Ersatzteile selber machen: Ersatzteil rekonstruieren mit Blender (8 Bilder)

Dann wies ich dem kopierten Hirsch einen Boolean-Modifier vom Typ "Difference" und als "Object" den Würfel zu und wandte den Modifier an. Dasselbe dann nochmal von der anderen Seite der Geweihstange, wobei man den in Ort und Rotation passend angepassten Würfel als Differenzobjekt wiederverwenden kann.
Das Ergebnis des Verfahrens ist ein geschlossenes Mesh, das ein Ausschnitt aus der rechten Geweihstange samt herausragender Mittelsprosse umfasst. Das wiederum lässt sich mittels "Object/Mirror/X Global" spiegeln und auf die andere Seite bringen.
Feinarbeit
Ziel ist es jetzt, diese gespiegelte Kopie des entscheidenden Stücks der linken Geweihstange als Rohling für das Ersatzteil für die rechte Seite über Rotation und Verschiebung so mit dem gescannten Bestand Deckung zu bringen, dass man am Ende wieder mittels Boolean Modifier im "Difference"-Modus das eine Objekt vom anderen abziehen kann und eine neue Mittelsprosse samt exakt zur Bruchfläche passendem Ende bekommt. Da der Hirsch bei genauer Betrachtung alles andere als symmetrisch ist, passt das gespiegelte Objekt nicht auf Anhieb. Und auch nach allerlei Hin- und Herschieben und -drehen muss man am Ende an die einzelnen Knoten (Vertices) des Oberflächennetzes (Mesh) ran.
Wegen der fantastischen Scan-Auflösung besteht das Mesh selbst des kleinen Ersatzteilrohlings aus sehr vielen Knoten, was die Arbeit mühsam macht. Auf der anderen Seite ist eine so fein in Facetten aufgelöste Oberfläche gar nicht nötig, weil der 3D-Drucker das später ohnehin nicht so präzise reproduziert. Insofern ist das der richtige Moment, das Mesh und sich die Arbeit zu vereinfachen, mittels eines Decimate-Modifiers mit der Ratio 0,05, der die Zahl der Knoten um den Faktor 20 senkt. Anschließend ist es relativ einfach, wie auf Bild 6 in der Bilderstrecke zu sehen, die Knoten des Rohlings nahe der Bruchstelle so zu verschieben, dass anschließend ein Boolean-Modifier im Modus "Difference" den Rohling exakt passend zur gescannten Bruchstelle zurechtstutzt. Was an anderer Stelle nach Anwenden des Modifiers als Restgeometrie noch irgendwo an frei schwebender Mesh-Reste übrig bleibt, kann man einfach wieder mit dem in der ersten Bilderstrecke gezeigten Trick entfernen.
Wie im letzten Bild der zweiten Bilderstrecke zu sehen, habe ich dem Ersatzteil noch einen Handgriff in Form eines langen, schmalen Keils spendiert, der nur an zwei Stellen am Ersatzteil sitzt, der aber im Druck als Stütze und später beim Kleben als Griff dienen kann.
Drucken, kleben und vergolden
Spätestens jetzt stand eine bisher aufgeschobene Entscheidung an: Wie wollte ich die Reparatur hinterher kaschieren? Klar war, irgendeine hirsch-ähnliche fertige Filamentfarbe kam nicht in Frage, das wäre wahrscheinlich ebenso auffällig wie die Bruchstelle vorher und zudem hässlich. Dann dachte ich an möglichst neutrales Filament und eine kaschierende Bemalung – das wäre aber nochmal zusätzlich aufwändig geworden und solche Reparaturen verraten sich oft dadurch, dass die neue Farbe anders glänzt als die restliche Oberfläche des Objekts.
Meine Frau brachte dann die japanische Tradition des Kintsugi ins Spiel: Dabei wird bei der Reparatur Kitt mit Goldflocken oder -pulver verwendet, um den Schaden nicht zu verstecken, sondern nachgerade zu betonen. Das gefiel mir gut für meinen Hirsch, ihm nach all den Jahren eine goldene Mittelsprosse zu gönnen. Mein Lieblingsfilament mit Metalleffekt ist Extrudr BioFusion in der Farbe Steampunk Copper, aber das ließ sich leider nicht in der benötigten Schichtfeinheit drucken, weder auf dem Prusa i3 MK3S noch auf dem AnkerMake MC5 in der Redaktion. Der Ultimaker 2+ produzierte aus goldenem Innofil etwas eigentlich brauchbares, versenkte das Ende des Ersatzteils allerdings in einem amorphen Blob, der sich vom restlichen Druck nicht mehr lösen ließ.
Ersatzteile selber machen: 3D-Druck, Montage und Finish (3 Bilder)
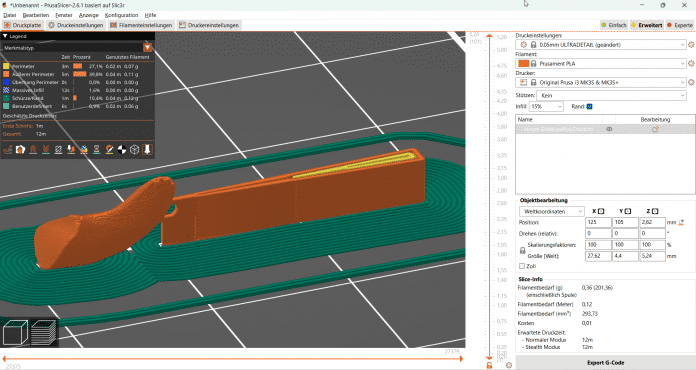
Das Rennen machte schließlich der AnkerMake mit Mystic Silky PLA Lila Gold von Redline Filament (siehe Bilder 2 und 3 der Bilderstrecke). Dass dieses Material tatsächlich nur von einer Seite golden und von der anderen violett(!) ist, störte mich da schon nicht mehr, denn alle goldenen Filamente waren mir nicht golden genug und ich war fest entschlossen, da noch mit dem glänzendsten Lack dranzugehen, den ich bekommen konnte.
Kleben
Vor dem Vergolden musste das Ersatzteil aber erst angeklebt werden (sonst hätte ich nach dem Entfernen des Griffes hinterher zumindest an die Trennstellen noch mal rangehen müssen). Im ersten Versuch benutzte ich den speziellen Kunststoffkleber UHU Allplast und konnte mein Ersatzteil schön passgenau platzieren und mittels des Griffes bequem andrücken. Nach dem Trocknen entfernte ich den Griff mit einem Seitenschneider und ging noch mit etwas Schleifpapier über die Schnittstellen, dabei passierte es: Die neue Sprosse löste sich wie nichts vom alten Geweih. Der verwendete Kleber hielt zwar auf dem PLA meines Ersatzteils, aber das genaue Material des Hirschs ist mir unbekannt. Ich ging bisher von Kunststoff aus, aber es könnte auch eine besonders feste und feine Keramik sein.
Zweiter Versuch: Sekundenkleber, jetzt ohne Griff. Das hat geklappt. Und rein von der Form her sah das schon ziemlich gut aus.
Vergolden
Da brauchbarer Goldlack fürs Finish nicht vorhanden war, ging ich in den Künstlerbedarfsladen der Wahl und ließ mich beraten. Eigentlich suchte ich eine kleine Menge Lack, die man mit einem Pinsel auftragen und möglichst hinterher noch polieren konnte – am Ende kam ich aber mit einem Starter-Set für Echtvergoldung mit Blattgold heraus. Das war am Ende auch nicht viel teurer als eine Sprühdose sehr hochwertigen Goldlacks, von dem ich nur eine winzige Menge benötigt hätte und der sich niemals gezielt nur auf mein Ersatzteil hätte auftragen lassen ...
Die Methode des Herstellers des Vergolder-Kits ist tatsächlich relativ einfach: Man trägt auf die zu vergoldende Fläche einen speziellen Lack auf Wasserbasis auf und lässt den trocknen. Dann pinselt man einen speziellen Aktivator auf die Fläche, lässt den ebenfalls trocknen und drückt das Blattgold auf. Das befindet sich auf einem Transferpapier, ähnlich wie Aufreibebuchstaben. Zum Schluss drückt man das Gold mit einem speziellen Poliertuch an und bringt es gleichzeitig auf Glanz.
Der Lack ist relativ dickflüssig und soll auch nicht zu dünn aufgetragen werden – er hat auch die in meinem Fall angenehme Eigenschaft, kleine Unebenheiten in der Oberfläche zu füllen. Ich entschied mich für eine optionale zweite Lackschicht nach komplettem Aushärten der ersten, damit sich nicht am Ende die Materialschichten aus dem 3D-Druck durch das Gold abzeichnen.
Das Vergolden selbst war dann doch spannend, denn einmal vom Transferpapier gelöst, ist die hauchdünne Goldfolie schwer zu bändigen. Aber es klappte dann doch im ersten Versuch sehr gut. Etwas gewöhnungsbedürftig ist, dass sich spätestens beim Polieren das nicht verklebte Gold in winzigen bis größeren Flocken löst, den Arbeitsplatz sprenkelt und erstaunlich gut auf Oberflächen haftet – beim nächsten Mal würde ich auf meinen Arbeitstisch statt der Schneidematte als Unterlage ein Stück Papier legen, das ich hinterher wegwerfen kann.
Damit war ich fertig und stolz und der Hirsch prangt in nie dagewesener Pracht an seinem angestammten Platz oben an der Gastherme. Die Goldsprosse sieht zwar nicht aus wie gegossen und perfekt poliert, gewisse Unebenheiten des 3D-Drucks im Inneren sind durchaus erkennbar. Ich denke aber, dass sich ein zu perfektes Goldstück zu sehr vom Rest des Hirschs abheben würde, um beides noch als eine Einheit wahrzunehmen. Die Vergoldung soll sogar wetterfest sein, verspricht der Hersteller des Lacks, das werde ich aber erst mal nicht ausprobieren. (pek)